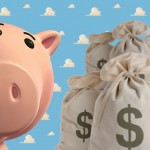
Building/Renovating A Warehouse Without Breaking The Bank
Let’s face it. Most manufacturing and production businesses now should have a warehouse. With the demand that the consumer industry asks and needs, a business should always be prepared. But truth be told, it’s not always that easy to get a warehouse.
Yes, there are now businesses out there that provide third-party warehousing services. But if you want to have your own warehouse or planning to renovate one, it’s going to cost you some major damage on your pockets. That’s why we assembled some tips on building or renovating a warehouse to ponder on without breaking the bank.
• A typical warehouse consists of eight areas: concrete, steel, earthwork, site utilities, roofing, general conditions, fire protection, and design fees. The key here is to focus on managing expenses on the major areas, and don’t sweat the petty costs. Major areas may include concrete which will be the whole building itself or for building a new warehouse and steel, for internal support and for storage racks. Earthwork for solid ground foundation. Depending on your preference, weigh in the eight areas on what will be considered a major need for the warehouse.
• This may seem weird, but small buildings are more expensive than bigger ones. A big warehouse will be cost-effective, since the small-foot costs of warehouses are in a parabolic curve.
• Show appreciation for your drivers by adding a decent deceleration lane and a wide curve by the warehouse entry.
• Find a building site that is flat so costs for earthwork will be cut down.
• Put the building on an area near the street so that the distance between the water source and drainage areas is reduced.
• Put the building project to a bid among several top designers or builders. Pick the one with the design that will put your building on its optimum use.
• Steel is one of the most widely used materials not only in warehouses but construction, in general. It is used in internal support, as storage form if preferring to employ light duty racking system, or as a major component in warehouse racking systems, especially here in the Philippines. Manage steel costs by favoring a steel design 3.5 pounds or less per square foot.
• Favor a white roof over other roof colors. Choosing a white roof reflects the sun’s rays, keeping the building cool, and minimizing costs on coolers.
• Invest in high volume but low speed fans to improve circulation of air, therefore, letting workers feel comfortable with their work. This is advisable for non-air-conditioned warehouses.
These are just some tips to think through to be able to utilize the best use for your money in your warehousing needs. Anyway, you can always rent for third party warehousing. Just choose a warehouse that will cater to your storage needs suitably.
Source:
inboundlogistics.com
Tags: economical ways, steel, storage system, warehouse